拉深模按其工序顺序可分为首次拉深模和后续各工序拉深模,它们之间的本质区别是压边圈的结构和定位方式上的差异。按拉伸模使用的冲压设备又可分为单动压力机用拉深模、双动压力机用拉深模及三动压力机用拉深模,它们的本质区别在于压边装置的不同(弹性压边和刚性压边)。按工序的组合来分,又可分为单工序拉深模、复合模和级进式拉深模。此外还可按有无压边装置分为无压边装置拉深模和有压边装置拉深模等。下面将介绍几种常见的拉深模典型结构。
1一凸模; 2一定位板; 3一凹模; 4一下模座
图 4.6.1 无压边装置的首次拉深模
1.首次拉深模
(1) 无压边装置的首次拉深模
(图4.6.1)此模具结构简单,常用于板料塑性好,相对厚度时的拉深。工件以定位板 2 定位,拉深结束后的卸件工作由凹模底部的台阶完成,拉深凸模要深入到凹模下面,所以该模具只适合于浅拉深。

(2) 具有弹性压边装置的首次拉深模
这是最广泛采用的首次拉深模结构形式(图4.6.2)压边力由弹性元件的压缩产生。这种装置可装在上模部分( 即为上压边 ) ,也可装在下模部分( 即为下压边 ) 。上压边的特征是由于上模空间位置受到限制,不可能使用很大的弹簧或橡皮,因此上压边装置的压边力小,这种装置主要用在压边力不大的场合。相反,下压边装置的压边力可以较大,所以拉深模具常采用下压边装置。
(3) 落料首次拉深复合模
图 4.6.3 为在通用压力机上使用的落斜首次拉深复合模。它一般采用条料为坯料,故需设置导料板与卸料板。拉深凸模 9 的顶面稍低于落料凹模 10 ,刃面约一个料厚,使落料完毕后才进行拉深。拉深时由压力机气垫通过顶杆 7 和压边圈 8 进行压边。拉深完毕后靠顶杆 7 顶件,卸料则由刚性卸料板 2 承担。
1一凸模; 2一上模座; 3一打料杆; 4一推件块; 5一凹模;
6一定位板; 7一压边圈; 8一下模座; 9一卸料螺钉
图 4.6.2 有压边装置的首次拉深模
(4) 双动压力机上使用的首次拉滦模
(图 4.6.4) 因双动压力机有两个滑块,其凸模 1 与拉深滑块( 内滑块 ) 相连接,而上模座 2(上模座上装有压边圈3) 与压边滑块(外滑块)相连。拉深时压边滑块首先带动压边圈压住毛坯,然后拉深滑块带动拉深凸模下行进行拉深。此模具因装有刚性压边装置,所以模具结构显得很简单,制造周期也短,成本也低,但压力机设备投资较高。
2.后续各工序拉深模
后续拉深用的毛坯是已经过首次拉深的半成品筒形件,而不再是平板毛坯。因此其定位装置、压边装置与首次拉深模是完全不同的。后续各工序拉深模的定位方法常用的有三种:第一种采用特定的定位板(图4.6.5) ;第二种是凹模上加工出供半成品定位的凹窝;第三种为利用半成品内孔,用凸模外形或压边圈的外形来定位(图4.6.6) 。此时所用压边装置已不再是平板结构,而应是圆筒形结构。
1-导料板;2-卸料板;3-打料杆;4-凸凹模;5-上模座;
6-下模座;7-顶杆;8-压边圈;9-拉深凸模;10-落料凹模
图 4.6.3 落料拉深复合模
1-凸模;2-上模座;3-压边圈;4-凹模;5-上模座;6-顶件块
图 4.6.4 双动压力机上使用的首次拉深模
图 4.6.5 无压边装置的后续工序拉深模
图 4.6.6 有压边装置的后续各工序拉深模
(1) 无压边装置的后续各工序拉深模
(图 4.6.5)此拉深模因无压边圈,故不能进行严格的多次拉深,用于直径缩小较少的拉深或整形等,要求侧壁料厚一致或要求尺寸精度高时采用该模具。
(2) 带压料装置的后续各工序拉深模
(图 4.6.6)此结构是广泛采用的形式。压边圈兼作毛坯的定位圈。由于再次拉深工件一般较深,为了防止弹性压边力随行程的增加而不断增加,可以在压边圈上安装限位销来控制压边力的增长(参见图 4.5.8)。
4.6.2 拉深模工作部分的结构和尺寸
拉深模工作部分的尺寸指的是凹模圆角半径凸模圆角半径

,凸、凹模的间隙 c ,凸模直径

,凹模直径

等,如图 4.6.7 所示。

1.凹模圆角半径
拉深时,材料在经过凹模圆角时不仅因为发生弯曲变形需要克服弯曲阻力,还要克服因相对流动引起的摩擦阻力,所以的大小对拉深工作的影响非常大。主要有以下影响:
(1) 拉深力的大小
小时材料流过凹模时产生较大的弯曲变形,结果需承受较大的弯曲变形阻力,此时凹模圆角对板料施加的厚向压力加大,引起摩擦力增加。当弯曲后的材料被拉入凸、凹模间隙进行校直时,又会使反向弯曲的校直力增加,从而使筒壁内总的变形抗力增大,拉深力增加,变薄严重,甚至在危险断面处拉破。在这种情况下,材料变形受限制,必须采用较大的拉深系数。

(2) 拉深件的质量
过小时,坯料在滑过凹模圆角时容易被刮伤,结果使工件的表面质量受损。而当

太大时,拉深初期毛坯没有与模具表面接触的宽度加大(图4.6.8) ,由于这部分材料不受压边力的作用,因而容易起皱。在拉深后期毛坯外边缘也会因过早脱离压边圈的作用而起皱,使拉深件质量不好,在侧壁下部和口部形成皱褶。尤其当毛坯的相对厚度小时,这个现象更严重。在这种情况下,也不宜采用大的变形程度。

(3) 拉深模的寿命
小时,材料对凹模的压力增加,摩擦力增大,磨损加剧,使模具的寿命降低。所以

的值既不能太大也不能太小。在生产上一般应尽量避免采用过小的凹模圆角半径,在保证工件质量的前提下尽量取大值,以满足模具寿命的要求。通常可按经验公式计算:

(4.6.1)
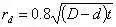
式中 d 为毛坯直径或上道工序拉深件直径 (mm) ; d 为本道拉深后的直径 (mm) 。首次拉深的可按表 4.6.1 选取。

后续各次拉深时应逐步减小,其值可按关系式

确定,但应大于或等于

。若其值小于

,一般很难拉出,只能靠拉深后整形得到所需零件。

表 4.6.1 首次拉深的凹模圆角半径

注:表中数据当材料性能好,且润滑好时可适当减小。
2.凸模圆角半径

凸模圆角半径对拉深工序的影响没有凹模圆角半径大,但其值也必须合适.
太小,拉深初期毛坯在

处弯曲变形大,危险断面受拉力增大,工件易产生局部变薄或拉裂,且局部变薄和弯曲变形的痕迹在后续拉深时将会遗留在成品零件的侧壁上,影响零件的质量。而且多工序拉深时,由于后继工序的压边圈圆角半径应等于前道工序的凸模圆角半径,所以当

过小时,在以后的拉深工序中毛坯沿压边圈滑动的阻力会增大,这对拉深过程是不利的。因而,凸模圆角半径不能太小。若凸模圆角半径过

大,会使

处材料在拉深初期不与凸模表面接触,易产生底部变薄和内皱,如图 4.6.8 所示。

一般首次拉深时凸模的圆角半径为:
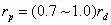
以后各次 可取为各次拉深中直径减小量的一半,即:

(4.6.2)
式中:为本道拉深的凸模圆角半径;

为本道拉深直径;

为下道拉深的工件直径。

图 4.6.8 拉深初期毛坯与凸模、凹模的位置关系
最后一次拉深时应等于零件的内圆角半径值,即:


但不得小于料厚。如必须获得较小的圆角半径时,最后一次拉深时仍取

,拉深结束后再增加一道整形工序,以得到

。

3.凸模和凹模的间隙

拉深模间隙是指单面间隙。间隙的大小对拉深力、拉深件的质量、拉深模的寿命都有影响。若值太小,凸缘区变厚的材料通过间隙时,校直与变形的阻力增加,与模具表面间的摩擦、磨损严重,使拉深力增加,零件变薄严重,甚至拉破,模具寿命降低。间隙小时得到的零件侧壁平直而光滑,质量较好,精度较高。

间隙过大时,对毛坯的校直和挤压作用减小,拉深力降低,模具的寿命提高,但零件的质量变差,冲出的零件侧壁不直。因此拉深模的间隙值也应合适,确定时要考虑压边状况、拉深次数和工件精度等。其原则是:既要考虑板料本身的公差,又要考虑板料的增厚现象,间隙一般都比毛坯厚度略大一些。采用压边拉深时其值可按下式计算:

(4.6.3)

式中μ为考虑材料变厚,为减少摩擦而增大间隙的系数,可查表 4.6.2 ;
表 4.6.2 增大间隙的系数μ
注:表中数值适用于一般精度(自由公差)零件的拉深。具有分数的地方,分母的数值适用于精密零件( it10--12 级)的拉深。
表 4.6.3 有压边时的单向间隙
注: 1. ——材料厚度,取材料允许偏差的中间值。

2. 当拉深精密工件时,对最末一次拉深间隙取

为材料的名义厚度;

材料的最大厚度,其值位

其中

为材料的正偏差。不用压边圈拉深时,考虑到起皱的可能性取间隙值为:


式中较小的数值用于末次拉深或精密拉深件,较大的值用于中间拉深或精度要求不高的拉深件。
在用压边圈拉深时,间隙数值也可以按表 4.6.3 取值。
对精度要求高的零件,为了使拉深后回弹小,表面光洁,常采用负间隙拉深,其间隙值为,
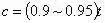
处于材料的名义厚度和最小厚度之间。采用较小间隙时拉深力比一般情况要增大20%,故这时拉深系数应加大。当拉深相对高度

的工件时,为了克服回弹应采用负间隙。

4.凸模、凹模的尺寸及公差
工件的尺寸精度由末次拉深的凸、凹模的尺寸及公差决定,因此除最后一道拉深模的尺寸公差需要考虑外,首次及中间各道次的模具尺寸公差和拉深半成品的尺寸公差没有必要作严格限制,这时模具的尺寸只要取等于毛坯的过渡尺寸即可。若以凹模为基准时,凹模尺寸为:

凸模尺寸为
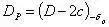
对于最后一道拉深工序,拉深凹模及凸模的尺寸和公差应按零件的要求来确定。
当工件的外形尺寸及公差有要求时(如图 4.6.9a 所示) ,以凹模为基准。先确定凹模尺寸因凹模尺寸在拉深中随磨损的增加而逐渐变大,故凹模尺寸开始时应取小些。其值为:(4.6.4)
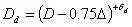
凸模尺寸为: (4.6.5)

当工件的内形尺寸及公差有要求时( 如图 4.6.9b 所示 ) ,以凸模为基准,先定凸模尺寸。考虑到凸模基本不磨损,以及工件的回弹情况,凸模的开始尺寸不要取得过大。其值为: (4.6.6)
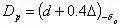
凹模尺寸为: (4.6.7)

凸、凹模的制造公差和

可根据工件的公差来选定。工件公差为 itl3 级以上时,

和

可按it6~8 级取,工件公差在itl4 级以下时,

和

按 itl0 级取。

图 4.6.9 拉深零件尺寸与模具尺寸
a) 外形有要求时 ;b) 内形有要求时
5.凸、凹模的结构形式
拉深凸模与凹模的结构形式取决于工件的形状、尺寸以及拉深方法、拉深次数等工艺要求,不同的结构形式对拉深的变形情况、变形程度的大小及产品的质量均有不同的影响。
当毛坯的相对厚度较大,不易起皱,不需用压边圈压边时,应采用锥形凹模(参见图 4.2.4) 。这种模具在拉深的初期就使毛坯呈曲面形状,因而较平端面拉深凹模具有更大的抗失稳能力,故可以采用更小的拉深系数进行拉深。
当毛坯的相对厚度较小,必须采用压边圈进行多次拉深时,应该采用图 4.6.10 所示的模具结构。图 4.6.10a 中凸、凹模具有圆角结构,用于拉深直径的拉深件。图4.6.10b中凸、凹模具有斜角结构,用于拉深直径 d ≥ 100mm 的拉深件。

图 4.6.10 拉深模工作部分的结构
采用这种有斜角的凸模和凹模,除具有改善金属的流动,减少变形抗力,材料不易变薄等一般锥形凹模的特点外,还可减轻毛坯反复弯曲变形的程度,提高零件侧壁的质量,使毛坯在下次工序中容易定位。不论采用哪种结构,均需注意前后两道工序的冲模在形状和尺寸上的协调,使前道工序得到的半成品形状有利于后道工序的成形。比如压边圈的形状和尺寸应与前道工序凸模的相应部分相同,拉深凹模的锥面角度也要与前道工序凸模的斜角一致,前道工序凸模的锥顶径

应比后续工序凸模的直径

小,以避免毛坯在 a 部可能产生不必要的反复弯曲,使工件筒壁的质量变差等(图4.6.11) 。

图 4.6.11 斜角尺寸的确定
图 4.6.12 最后拉深中毛坯底步尺寸的变化
为了使最后一道拉深后零件的底部平整,如果是圆角结构的冲模,其最后一次拉深凸模圆角半径的圆心应与倒数第二道拉深凸模圆角半径的圆心位于同一条中心线上。如果是斜角的冲模结构,则倒数第二道工序(道)凸模底部的斜线应与最后一道的凸模圆角半径 相切,如图 4.6.12 所示。

凸模与凹模的锥角对拉深有一定的影响。

大对拉深变形有利,但

过大时相对厚度小的材料可能要引起皱纹,因而

的大小可根据材料的厚度确定。一般当料厚为 0.5--1.0mm ;当料厚为 1.0~2.0mm 时

为了便于取出工件,拉深凸模应钻通气孔,如图 4.6.10 所示。其尺寸可查表 4.6.4 。
表 4.6.4 通气孔尺寸
拉深模具的构造:向下拉深首次拉深模
在带可动式压边圈的拉深下出料构造的模具内设置了顶出装置的构造。其构造如【图】所示。
该构造既可用于从坯料拉深带凸缘的圆筒,也可用于拉深无凸缘的圆筒。而且,由于是用凸模和顶出装置夹着材料进行加工,因此拉深底部的平面度较好。顶出装置具有压料和排出凹模中制件的2种功能。
该构造的缺点是不适于进行较深的拉深加工。因为受到可装入弹簧的长度限制。在上模方面,凸模与拉深深度成比例变长。同时,压边用弹簧也必须变长。如果根据弹簧的变形量来决定弹簧长度,有时候所需长度空间比凸模还要长,上模变大,考虑与下模的平衡关系、模具闭合高度等因素,构造很难成立,甚至于无法实现。
这同样也适用于下模的顶出装置的弹簧。
考虑弹簧空间的影响,这种构造经常用于较浅的拉深。
拉伸类模具拉伤的具体解决方法
从冲压作业的角度来看这种模具,其作业性不算理想。进行说明的话,材料装入下模的定位装置中。上模下降进行拉深加工。加工得到的制件在被顶出装置和上模的压边圈夹持的状态下自凹模排出,但由于压边圈压紧制件,制件残留在凹模上。需由作业人员取出制件,然后将材料装入模具内。作业人员需要进行将材料插入模具内和从模具内取出制件等两个作业步骤,与仅需将拉深下出料的材料放入模具内的加工过程相比,其作业效率有所下降。
设计连续模具的注意事项:
1、要合理地确定工步数:连续模的工步数等于分解的单工序之和,如冲孔—落料连续模的工步数,通常是等于冲孔与落料两个单工序之和。但为了增加冲模的强度和便于凸模的安装,有时可根据内孔的数量分几步完成。其工步数的确定原则,主要是在不影响凹模强度的原则下,其工步数选用得越少越好,工步数越少,累积误差越小,则所冲出的工件尺寸精度越高。
2、在冲孔与落料工序次序安排时,应把冲孔工序放在前面,这样不但可以确保带料的直接送进,而且又可借助冲好的孔来作为导正定位孔,以提高工件的精度。但在与某些弯曲后的尺寸或某突出部分位置成关联尺寸时,就要根据实际确定冲孔的位置。
3、在没有圆形孔的工件中,为了提高送料步距的精度,可以在凹模的首次步序中设计有工艺孔,以使此工艺孔作为导正定位,提高冲件精度。但作为现在的模具设计中,我们对一些精密件的冲压已经逐步或全部采用了外框式的导料带。这样有利于保证复杂工件的加工精度。
4、同一尺寸基准的精度要求较高的不同孔,在不影响凹模强度的情况下,应安排同一工步成形。
5、尺寸精度要求较高的工步,应尽量安排在最后一工序,而精度要求不太高的工步,则最好安排在较前一工序,这是因为工步越靠前,其积累误差越大。
6、在多工步的连续模具中,台冲孔、切口、切槽、弯曲、成形、切断等工步的安排次序,一般应把分离工序如冲孔、切口、切槽安排在前面,接着可安排弯曲、拉深成形工序,最后再安排切断及落料工序。
7、冲不同形状及尺寸的多孔工序时,尽量不要把大孔与小孔同时放在同一工步上,以便修模时能确保孔距精度。
8、在设计时,若成形及冲裁在同一冲模上完成,则成形凸模与冲裁凸模应分别固定,面不要固定在同一固定板上。尽量把成形凸模固定在脱板上面。后面加装背板。
9、在设计时,一定要使各工步已成形部分不受破坏,使带料保持在同一送料线上。
10、对于工序步数很多且带有较多弯曲工步的模具,其凹模刃口应尽量采用入块结构,可实现快速更换和修磨。
11、针对凸模的固定方式,在实现连续冲压时,要采用挂台和反压块的固定方式,以保证在连续冲压中不会发生凸模掉下而损坏模具的事项。切记!
12、在模具结构强度和位置允许的情况下。多工步的模具要尽量采用浮动导料销。
13、切边的接口形式。在连续模中,经验不足的人常会将接口做成清角,我建议采用半圆切口。
14. 在产品是基准孔的圆孔,一般情况下应在与导正孔同一工步冲切。如果圆孔边距比较小的时候而孔尺寸有要求,应先切外形,再冲孔。
补充一下:
1,在成型部位加微调有利于保证零件的重要尺寸,而不必装拆模具调整凸凹模尺寸
2,在模具中加误送装置以保证生产的安全性
3,在模具中加校平校扭以保证后续工序的进行
4,选择合理的导正、浮料方式有利于零件的成形
5,零件要有防误装措施,以免误装后打坏模具
如果对于本文,你还有不明白、不理解的地方,欢迎评论或私信,我将第一时间解答!
如果你是想往设计方向发展,可以加入我创建的千人模具设计社群一起学习、交流、探讨(无广告);群号824095992