Since the beginning of the 90s, the Institute for Robotics and Process Control deals with the development of robot control systems. Common industrial ones only provide inflexible interfaces, which hamper or inhibit possibilities of multi-sensor integration. For instance, Cartesian force/torque control requires low control cycle times - not only for appropriate control behavior but for short response times on control variable leaps (e.g. caused by sudden hard environmental contact). A transputer-based system was a first open control system approach, which was applied to work on manutec manipulators. The latest version is a PC-based system, which focuses on a modular software architecture ( MiRPA, hybrid robot control architectures). Based on these experiences, new architectures for the Stäubli RX-series and the TX-series are provided. Here, the excellent mechanical properties are combined with an open and flexible control architecture to create a base for venerable research results.
The picture below shows our open robot control system based on the Stäubli TX series with an CS8c controller employing a low-level interface (LLI) developed by Stäubli.
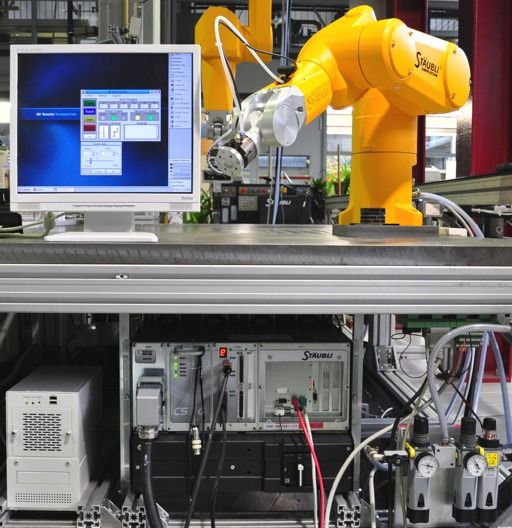
Open robot control architecture based on the Stäubli TX-series featuring CS8c controllers and the low-level interface (LLI).
Since the advent of affordable multi-core processors, our entire robot control system including demanding sensor data acquisition and processing can be incorporated into one powerful PC running the real-time operating system QNX. An architecture sketch of our system is shown in the figure below. In contrast to our open control architecture for the RX-series, no modifications of the controller hardware are necessary. This feature enables using our control architecture with virtually any TX-series manipulator providing a low-level interface - merely a USB flash drive containing the software for the CS8c controller and a PC equipped with the RTOS QNX are necessary.
In the following paragraphs our open robot control architecture for the Stäubli RX-series is described. An RX60 manipulator executing a sensor guided assembly task is shown on the picture below. Its control cabinet stands in the background. The human machine interface (HMI) is mounted with a pivot arm to the control cabinet and provides excellent possibilities for manual control and teach-in programming. Besides the most important operational controls a touch screen panel and a Space Mouse is available.
However, this work does not focus on a convenient HMI, but moreover on open interfaces, extensibility, scalability, robustness for external disturbances, and especially on the requirement to keep the usage of sensors entirely open. The above-mentioned possibilities for manual control a teach-in programming are only the necessary base.
Unless parts of the original control system match the new requirements, the parts are reused in the new system. Essentially, the power electronics, i.e. the frequency inverters and their accessories, have to be mentioned here. For manipulator operation, at least one control PC is required. A motion control board within this PC constitutes the interface to an electronic adaptation assembly, which delivers velocity set points to each frequency inverter on the one hand side, and which provides the joint positions to the control computer. In addition, I/O ports for further periphery (brakes, inverter control, valves, etc.) are provided. One major requirement is to make the absolute manipulator position permanently available to the controller. Therefore, an electronic assembly group for position tracking was developed. This one transmits the current position with an accuracy of 13 Bit via the serial port to the control PC. To guarantee the board's functionality at AC power failures and during transports, the position-tracking unit supplied by accumulators if required. The communication vie the serial port occurs only at during the start-up procedure, afterwards, die control computer receives the position information from the motion control board.
To assure an excellent dynamic behaviour, signal quality loss and signal latency have to be kept small, such that the necessary bandwidth of the components for signal adaptation between PC and drive electronic was determined preliminary to the development. Interfaces to the control computer are such open, that the user can freely decide how to design his software architecture. The signals for basic manipulator control are only the joint velocity set points for the drive controllers and the position inputs.
The proposed architecture uses a joint position controller, which is provided as interface to higher software layers. Besides the possibility to run all processes (joint position control, hybrid control, trajectory planning, user application, etc.) on one machine, is it useful to swap further processes out to other PCs and to take a real time communication system between them.
To follow the introductory mentioned aim of multi-sensor integration, the following figure depicts a suggestion for a possible architecture:
Further information may be found in our Publications. In case of any further questions please contact Daniel Kubus.